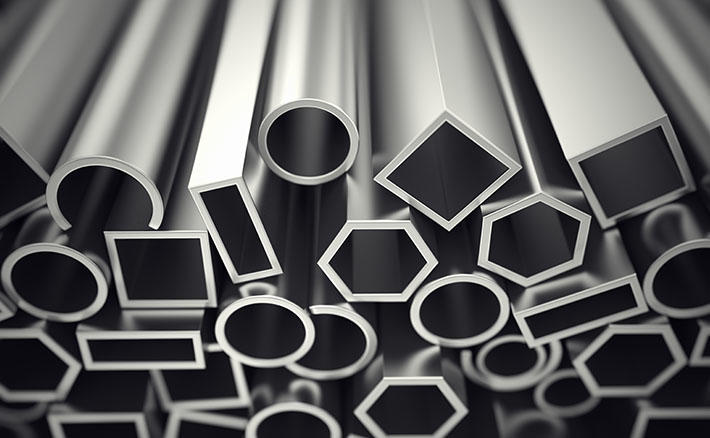
Perché le leghe di alluminio sono chiamate anche “leghe leggere”
Le leghe di alluminio sono comunemente note anche come leghe leggere per via del loro peso specifico, che è appunto ridotto. La leggerezza è la principale dell’alluminio: il suo peso specifico è pari a 2,7 Kg/dm3, a parità di volume pesa un terzo dell’acciaio. È inoltre un materiale con un’ottima resistenza e una notevole lavorabilità e, per questi motivi, è largamente utilizzato in molti settori, in particolare in quello aeronautico, basti pensare che gli aeroplani per circa il 70% sono costituiti di alluminio.
L’alluminio è sempre più impiegato anche nel settore edilizio e strutturale perché alla leggerezza abbina un’ottima resistenza strutturale che permette di progettare costruzioni diminuendo i carichi. L’alluminio è utilizzato anche per le finiture a viste, essendo particolarmente resistente alla corrosione atmosferica: si ricopre infatti di uno strato di ossido protettivo che reagisce con l’ossigeno atmosferico e lo rende impermeabile. Esiste però un difetto nell’alluminio, ovvero la carenza di rigidezza, che viene mitigata o del tutto cancellata con la fusione assieme ad altri metalli quali zinco, rame, nichel, magnesio e silicio: da queste fusioni derivano le cosiddette leghe leggere.
Pregi e difetti delle leghe leggere
Le leghe leggere sono quindi costituite principalmente di alluminio e, secondariamente, da altri materiali in grado di completarne le caratteristiche. L’opportuna scelta della combinazione nelle leghe di alluminio consente di ottenere leghe leggere con ottime proprietà meccaniche e di resistenza alla corrosione. È inoltre fondamentale la scelta dei parametri termici quali la temperatura di fusione e i tempi di permanenza nel processo di fusione.
In sostanza, per limitare i difetti e ampliare le possibilità di utilizzo dell’alluminio si possono creare leghe leggere grazie ad altri elementi che ne migliorano le proprietà meccaniche e lo rendono particolarmente diffuso in tutti i settori, non solo in quello aeronautico.