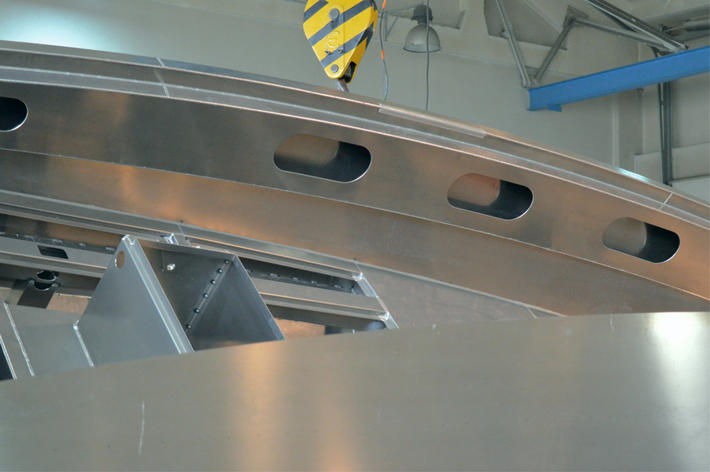
Le leghe di alluminio per il settore navale
Da molti decenni l’uso dell’alluminio nelle imbarcazioni è una realtà in crescita, e questo perché il metallo leggero riesce a mediare molto bene le esigenze del progettista, del costruttore e dell’utilizzatore finale. A ciò si aggiunge l’intrinseca sostenibilità ambientale dell’alluminio che lo rende il materiale di prima scelta per i più innovativi progetti ecosostenibili di imbarcazioni da diporto e commerciali.
L’alluminio è uno dei quattro materiali base per la costruzione navale, insieme al legno, all’acciaio e ai materiali compositi della famiglia GRP (Glass Reinforced Plastics). Il legno è stato il materiale protagonista in questo tipo di applicazione sino alla fine dell’800, oggi viene scelto quasi unicamente per naviglio speciale, come ad esempio yacht di fascia alta. L’acciaio subentrò al legno in virtù di caratteristiche più attraenti, dalla resistenza meccanica, al costo, alla disponibilità, alla semplice lavorabilità, avendo limiti come l’elevata densità di volume e la modesta resistenza alla corrosione.
L’alluminio si affaccia come candidato all’impiego nelle costruzioni navali negli ultimi anni del XIX secolo, quando ancora la sua penetrazione in molti segmenti di applicazione era appena agli inizi. Chiaramente si impose all’attenzione degli operatori come materiale molto interessante per la costruzione navale a causa della leggerezza, del vantaggioso rapporto resistenza/peso e della eccellente resistenza alla corrosione. I compositi e le fibre rinforzate sono i materiali più recenti per gli impieghi nelle costruzioni navali, rispetto al tradizionale legno offrono significativi vantaggi, dalla bassa manutenzione alla buona resistenza alla corrosione.
È chiaro che i fattori che fanno preferire l’uno o l’altro dei diversi materiali sono numerosissimi, dalla dimensione delle imbarcazioni alle prestazioni previste, alla consistenza numerica delle serie da produrre.
L’alluminio, con i diversi tipi di leghe commerciali, esprime un equilibrio interessante di:
- Resistenza meccanica e agli urti;
- Leggerezza;
- Durabilità;
- Proprietà estetiche e funzionali;
- Sicurezza e affidabilità;
- Semplicità di lavorazione e manutenzione.
L’impiego dell’alluminio nella nautica e nel settore navale
Storicamente, si ricordano esperienze con l’alluminio agli inizi del secolo scorso, quando di questo materiale si sapeva molto poco. Già allora, però, il metallo nuovo, un po’ misterioso, suscitava curiosità e interesse perché leggero, bello a vedersi, resistente e inattaccabile dalla corrosione, quindi adatto a nuove soluzioni per un mezzo che si muove nell’acqua.
Si parla evidentemente di applicazioni di assoluta avanguardia, mentre per una reale penetrazione nel mercato bisogna attendere gli anni intorno al 1940, con l’impiego nei navigli militari di laminati di leghe da trasformazione plastica Al-Mg, conosciute nei cantieri con la denominazione commerciale Peraluman.
Oggi le leghe di alluminio sono ancora giovani, ma non hanno più nulla di misterioso: da anni si conoscono le prestazioni, le tecnologie e i metodi di lavorazione e finitura, oltre ai criteri di progettazione più adeguati agli impieghi nelle imbarcazioni da diporto, in quelle di uso commerciali e nei mezzi militari.
Le leghe storicamente di maggiore interesse per gli impieghi nel settore navale sono le composizioni della serie 5000 Al-Mg: presentano eccellente saldabilità e hanno un’elevata resistenza alla corrosione (specialmente in ambiente marino). Queste leghe trovano il loro caratteristico impiego come laminati. Ricordiamo che altre tipiche applicazioni delle leghe 5000 includono, oltre alle imbarcazioni, cartelli stradali, serbatoi criogenici, finiture decorative e architettoniche, barattoli ed elettrodomestici.
L’alluminio per applicazioni navali
Gli sviluppi successivi dell’utilizzo dell’alluminio nel settore navale furono le sovrastrutture delle navi mercantili, le barche da diporto e una diffusione capillare nelle attrezzature e accessori, in modo particolare come semilavorati estrusi.
Parliamo delle leghe 6000 Al-Mg-Si da estrusione, con buona formabilità a caldo, buona combinazione di proprietà e trattabili con un ciclo di bonifica semplice ed economico. Queste leghe hanno una composizione basata su diverse combinazioni degli alliganti principali magnesio e silicio, e sull’aggiunta di quantità minori di Cu, Mn e Cr. Nel complesso, presentano buone caratteristiche meccaniche, elevate doti di finitura superficiale, elevata resistenza alla corrosione, facile saldabilità.
Gli estrusi di alluminio hanno tante applicazioni perché quando al progettista serve un componente di forma intricata, caratterizzato da una sezione costante e da un certo sviluppo in lunghezza (particolarmente creativo sia dal punto di vista funzionale che da quello estetico), questo semilavorato risolve molti problemi.
Con la tecnologia dell’estrusione è infatti possibile riprodurre geometrie complesse, che la carpenteria tradizionale permetterebbe di ottenere solo a costi elevatissimi e con scarsa affidabilità di risultato: un esempio sono le sezioni usate per la realizzazione dei bottacci, spesso studiate anche per accogliere parti in gomma, laddove il contatto nave-banchina è continuo e non solo occasionale. In termini di complessità, gli estrusi chiusi sono l’esempio più eclatante, anche se le moderne tecnologie di giunzione (specialmente la saldatura laser) permettono oggi di produrre pannelli sandwich analoghi senza il ricorso all’estrusione e consentono anche di pensare gli stessi non necessariamente in lega leggera, ma anche in acciai alto-resistenziali di modesto spessore, divenuti competitivi sul piano tecnico-economico per applicazioni specifiche, come ponti garage, ponti volo e rampe.
Le leghe da fonderia e i getti per applicazioni navali
Infine, abbiamo le leghe da fonderia per getti, con molte tecnologie disponibili per soddisfare i requisiti imposti al componente. Ogni processo offre vantaggi e benefici ben precisi, soprattutto se utilizzato tenendo conto delle caratteristiche della lega da colare e della tipologia del componente da produrre.
Dal punto di vista metallurgico, per le leghe da fonderia valgono considerazioni analoghe a quelle per le leghe da lavorazione plastica. Esistono diverse famiglie di leghe, (quelle per impieghi nel settore marino sono sostanzialmente dei sistemi Al- Si eAl-Mg non trattabili termicamente, e Al-Si-Mg da trattamento termico) con diverse proprietà di fonderia (colabilità, suscettibilità al ritiro, fragilità), diverse caratteristiche meccaniche e differenti proprietà tecnologiche (lavorabilità all’utensile, resistenza in ambiente aggressivo, possibilità di finitura superficiale, saldabilità).
In conclusione, le leghe di alluminio trovano da anni applicazioni crescenti nel settore delle costruzioni navali. Il metallo leggero è ancora giovane ma le caratteristiche prestazionali, le tecnologie, i metodi di lavorazione e finitura e i criteri di progettazione sono più che noti.
Inoltre, l’alluminio è il materiale per il risparmio energetico, per la salvaguardia ambientale, la competitività economica, la soddisfazione e la sicurezza degli utenti finali. Si impone sempre di più nel campo dei trasporti e per questo ha espresso ottimi sviluppi nel navale.
Con il patrimonio di decenni di conoscenze dell’industria aeronautica e con l’urgenza dell’industria dell’auto di fabbricare mezzi più leggeri, meno inquinanti e socialmente sostenibili, si è creata in pochi anni una nuova cultura tecnologica per un’ampia diffusione dell’alluminio nei trasporti. Di questo processo, anche il settore delle imbarcazioni ha tratto un nuovo stimolo all’innovazione.
Fonte: A&L Aluminium Alloys Pressure Diecasting Foundry Tecniques