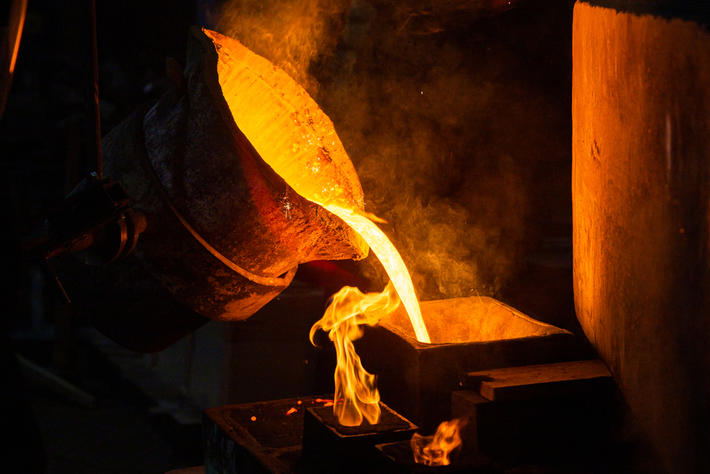
Prima produzione industriale di ZnAl15Cu1Mg
Dal 2014, quando furono eseguite le prime prove di pressocolata in camera calda con l’ipereutettico ZnAl15Cu1Mg nell’ambito del progetto di UNIBS & partner con la Regione Lombardia, sono stati effettuati numerosi test per gestire le varie questioni riguardanti la realizzazione di una macchina di pressocolata in camera calda adatta alla colata della lega.
Nel 2018, dopo la ripresa del progetto per la pressocolata in camera calda di ZnAl15Cu1Mg, lo Studio Olafur Eliasson ha effettuato la prova definitiva della fattibilità in un progetto artistico di MORI (WT), a Tokyo. La scelta di una lega di zinco è nata dall’idea di recuperare il metallo principale, lo zinco, dalle polveri dell’incenerimento domestico.
Poiché l’opera d’arte è un oggetto multi-volume sospeso a soffitto e deve essere antisismica, sono state effettuate numerose simulazioni meccaniche che hanno evidenziato la necessità di una lega più performante in termini di scorrimento viscoso (o creep) e resistenza meccanica, per cui la scelta è caduta sull’utilizzo della lega ZnAl15Cu1Mg rispetto alla classica lega di zinco per pressocolata.
Dopo aver verificato la stabilità della lega nella macchina di pressocolata in camera calda, sono state effettuate le colate di una serie di campioni di prova meccanica per verificarne le proprietà complessive. La riciclabilità della lega è stata dimostrata in un’altra serie, in modo da poter realizzare cicli di produzione normali.
La colata delle anime dell’oggetto d’arte ha evidenziato la possibilità di ampliare la gamma di applicazioni della lega di zinco colata in macchina a camera calda.
Introduzione sulla produzione industriale ZnAl15Cu1Mg
Dal 2018, dopo quattro anni di test intensivi sulle prestazioni della lega ZEP® 1510 in diverse condizioni nella macchina di pressocolata in camera calda, si è deciso di individuare il progetto adatto ad avviare una serie industriale completa. Ciò è stato realizzato unitamente a un progetto artistico dell’Art & design studio SOE di Berlino, con la creazione di una serie di quattro sculture in pressocolata da appendere al soffitto di un edificio di Tokio, in Giappone. Le sculture sono composte da 7000 corpi a undici facce. I singoli corpi sono pressofusi e dovrebbero essere realizzati in lega di zinco riciclato, ottenuto per elettrolisi dello zinco recuperato dalle polveri dell’incenerimento dei rifiuti domestici.
Risultato della pressofusione in camera calda di zinco e alluminio
Poiché l’opera d’arte è appesa a un soffitto, questioni come il peso sono estremamente determinanti nella scelta della lega da utilizzare per la pressocolata. Lo ZL5 (zamak5) classico ha una densità di circa 6,7 gr/cm³, per cui la scultura potrebbe subire uno scorrimento viscoso sotto il proprio peso. Per questo motivo, è stata scelta la nuova lega ZEP® 1510, che riduce il peso del 20% circa e presenta una resistenza allo scorrimento viscoso 100 volte superiore a temperatura ambiente. Il miglioramento della resistenza meccanica (20% in più rispetto allo Zamak 5) permetterebbe inoltre ai designer di ampliare il concept.
Prima di poter realizzare la serie, era tuttavia necessario effettuare ulteriori verifiche in fonderia, tra cui:
- La stabilità della lega durante un periodo di colata più lungo;
- Le proprietà meccaniche effettive della lega per garantirne la stabilità durante l’invecchiamento;
- La riciclabilità della lega che implica il riutilizzo dei canali di colata e le bavature delle colate.
Queste tre serie di colate sono state eseguite nel laboratorio di Oscar Frech GmbH.
In primo luogo, su una piccola macchina di pressocolata in camera calda Frech W20 con uno stampo a 12 cavità per verificare la colabilità della lega e individuare l’impostazione limite dei parametri. Ben presto (5000 iniezioni in totale in una settimana di colata) è apparso chiaro che la temperatura di colata dovesse essere aumentata a 530°C per rendere la lega sufficientemente fluida da consentire un buon riempimento della cavità.
Nel contempo, è stata verificata la capacità di riciclaggio utilizzando tre rapporti di peso tra materiale vergine e riciclabile (25% /50%e 100% di contenuto di materiale riciclato della colata). Sebbene la lega si mantenga stabile, il Fe aumenta a causa della contaminazione del contenuto del crogiolo quando si introduce una lega già riciclata che presenta una maggiore quantità di Fe. Le analisi sono state eseguite mediante analisi spettrale presso Grillo Werke AG su campioni prelevati in diverse parti del crogiolo.
La seconda serie è stata eseguita su una macchina di pressocolata in camera calda Frech W80, in modo da colare un numero sufficiente di campioni meccanici (2000 iniezioni) al fine di avviare un’accurata verifica delle prestazioni meccaniche e confrontarle con il normale materiale di pressocolata in camera calda Zamak 5.
Sono state verificate le proprietà meccaniche dei campioni piatti da 3 mm (UTS/R0,2%/modulo di elasticità/allungamento) con lega in condizione di colata, invecchiata artificialmente (2 ore a 105°C) e sottoposta a trattamento termico (4 ore a 150°C) rispetto alle stesse proprietà dello Zamak5. Nel contempo, la verifica delle proprietà durante l’invecchiamento naturale ha evidenziato una tendenza all’invecchiamento modesta rispetto a quella nota dello Zamak 5. L’invecchiamento dello ZEP® 1510 negli ultimi 3,5 anni appare lineare.
L’analisi ha quindi accertato che la lega è abbastanza stabile da iniziare le 10000 iniezioni richieste per ottenere il volume necessario per i corpi dell’opera d’arte di SOE.
La serie è stata fusa su Frech W125 con stampo a doppia cavità. Le condizioni di colata sono state impostate a una temperatura di 530°C per il crogiolo e di 170°C per lo stampo, con una velocità di iniezione che raggiunge i 40m/s al bocchello delle cavità. Ciò è stato effettuato contemporaneamente al riciclaggio dei canali di colata. Per limitare la perdita di temperatura, era necessario tagliare quanto prima i canali di colata per recuperare il calore residuo. Nel contempo, è stata controllata la stabilità della lega prelevando tre campioni al giorno in modo da garantire la qualità del prodotto fuso. L’intera colata della serie durerebbe oltre sei settimane e indicherebbe anche l’aggressività della lega rispetto al crogiolo, al collo d’oca, alle fasce elastiche e a tutte le apparecchiature immerse nella lega nel periodo in esame.
Lo studio ha verificato la stabilità dell’elemento di lega Al presente nella composizione della lega stessa e indica che quest’ultima può essere utilizzata ed è adatta alle apparecchiature a camera calda senza particolari rischi di decomposizione.
La prima serie di prodotti di colata su macchina di pressocolata in camera calda ha dimostrato che la lega ZEP® 1510 è utilizzabile a livello industriale. La lega si mantiene stabile purché tutte le parti immerse nel crogiolo siano protette con vernice ceramica. Le fasce elastiche devono essere considerate come materiale di consumo e hanno una durata di circa 1000 iniezioni. L’alta temperatura di fusione della lega nel crogiolo richiede un sistema di riscaldamento performante al fine di garantire l’apporto di calore necessario a fondere i lingotti di lega e stare al passo con la produzione.
Fonte: In Fonderia – ll magazine dell’industria fusoria italiana